从最基本的管理诉求来说,企业追求的是设备投入产出最大化,也就是追求设备利用和运营效率的最大化。从这个意义上来分析,我们就不难理解设备管理从'事后维修'发展到'预防维修'阶段的原动力。因为必须要解决好设备突发故障对生产计划的干扰和产品质量的负面影响,才有可能来谈论效率最大化的问题。所以说,如何有效'预防'突出故障的发生,就成为所有设备管理者首先要去思考和解决好的问题。
预防性维修理念的落地机制,包括较强制性的预防维修计划执行(计划预修制),以及以点检为基础的预防维修制。两者的结合,就是目前很多企业耳熟能详的'点检定修制'。虽然'点检定修制'被很多企业所熟悉,但在实际执行过程中,仍在存在着诸多的问题。包括预防性维修计划受生产安排影响而无法有效执行问题;预防性维修计划的时间周期和检修内容如何更合理的问题;点检人员的责任心、意识和能力对设备劣化把握的有效性问题;点检标准的要素齐备性以及点检项目的识别和判断问题;简单的定时维修对复杂设备故障无法有效防范问题等等。
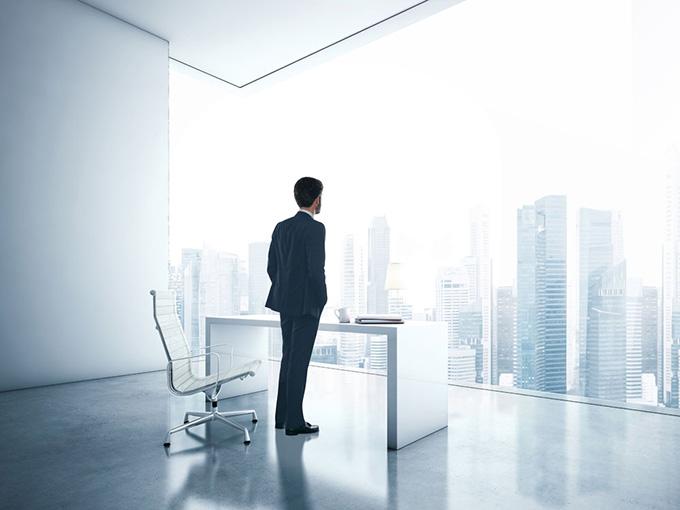
正是为了解决好这些问题,从上世纪70年代开始,人们就尝试不断引入新的故障现象识别技术和检查手段,来有效掌控设备劣化趋势和规律性。当然尽管早期一样由于受技术所限,对设备劣化趋势的掌控未必完全有效,但都逐步将基于时间的预防维修导向基于状态的预知维修(状态监测),都在不断丰富和完善着如何做到有效预防和预知故障的技术手段。
那么,是不是所有的设备都需要预防性维修呢?人们总是在实践中不断深化对事物本质的认识。在设备管理者通过不断加大维修投入(周期性的计划性预防维修队伍的人力成本和预先储备的零备件成本)来实现'预防性维修'的同时,也逐渐开始思考是不是所有的设备都需要实行'预防性维修'。并且对于很多类型的制造型企业来说,居高不下的维修费用和零备件资金占用,常常推高了生产成本而使产品丧失竞争力,所以企业管理层要求设备管理者如何降低维修费用就成了非常理所当然的事情,并且这种要求常常是在保障设备效率不降低的前期下提出的,这也成为衡量与评价企业设备管理核心价值的另一个重要方面。
鱼和熊掌如何兼得?如何在既要马儿跑得快身体好的同时少吃草?成为摆在设备管理者面前的绕不开的难题,我们必须为这种两难需求突破。
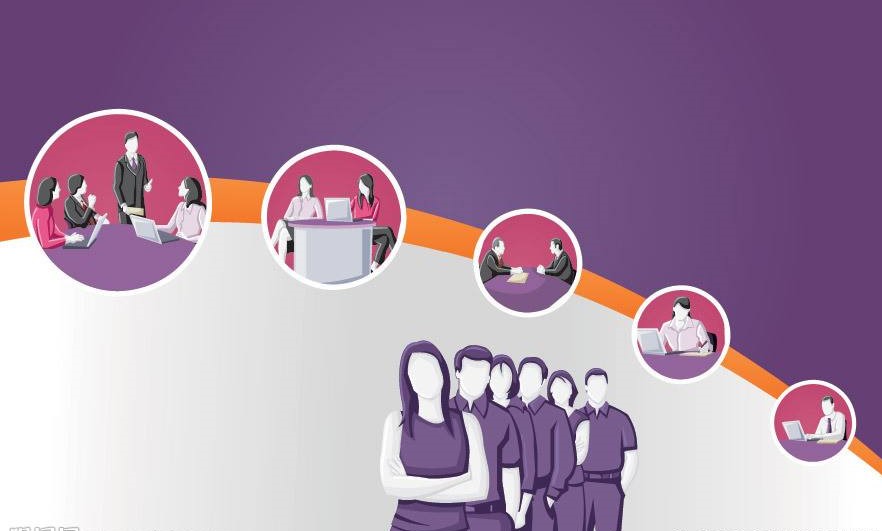
因为我们要关注'突发设备停机导致的损失'与'为了预防这类损失而做的投入'之间的平衡关系,所以任何一种极端做法都是不可取的。既然并不是所有的设备都需要做预防性维修,既然企业应该需求一种综合费用最优的模式,这里面就牵涉一个维修策略的应用问题。也就是说,需要根据设备故障特征进行分类,辅以不同的维修策略,以达到综合费用最优。'维修策略'的有效运用,就成为搞好设备管理应该把握的第二个关键。
当然维修策略不是简单地设定是事后维修还是预防维修,维修策略事实上非常丰富和多彩。如针对设备的设计缺陷展开'纠正性维修',即不拘泥于原设计而大胆尝试,解决一些重复发生的故障的根源性原因;再比如如何将一个设备的问题原因有效传递给设计方,或者类似机台,实现它机类比检修的问题(类似汽车厂商的召回机制)'维修预防'等等。这些多模式维修策略并存和综合应用,为设备管理者实现综合成本最优提供了大量有效手段。
文章来自网络,版权归作者所有,如有侵权请联系删除
“感谢冠卓咨询老师对项目组的全程辅导,通过做项目我们学会了如何用系统科学的方法分析研究问题;开阔了我们的视野并让我们的管理人员明白了团队协作的重要性。”
———北京某公司总经理 苏先生