这两天一直在忙于客户的流水线效率提升辅导,闲歇之际,总是对于改善过程中的经历回味总结,也禁不住想整理一下分享给网友们些许心得体会,共勉同进!
谈到生产线管理,我并不擅长,因为我相信更多一线生产干部或主管更有体会及经验,因为他们专职于生产现场的管理及改善,基于对产品工艺特性、人员个性、文化环境等诸多条件的熟识掌握,他们更能灵活把握管理的尺度与技巧。但回归到科学管理原理的理论基础,我们基于“作业方法”及“人性激发”这两个角度去展开改善,来浅析如何将工业工程改善手法应用到流水线管理中。
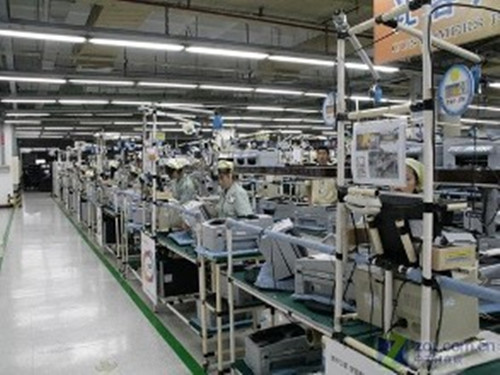
1、 了解流水线
第一条流水生产线于1914年诞生于美国福特公司,为福特公司带来金钱和名利上的巨大效益,它使得福特公司称霸于全球汽车行业乃至制造业。在这之前,福特公司的工人装配一个汽车地盘所需时间是12.5小时,而当流水线试验成功后,完成一件汽车底盘的装配时间是93分钟,劳动生产率提高了8倍多。
流水线是将工序分解后,分配给多人,依照工艺顺序作业完成的生产线,可以由机械动力传递,也可由人工直接传递等不同的方式,流水线的形状不限,可以“非”形、“一”形 、“U”形…等不同的方式体现,其作业方式可以是“坐式”作业,也可能是“站立”式作业,因不同产品及工艺区别可以为“装配型”流水线,也可以为“加工型”流水线。
2、 流水线常出现的问题
由于流水线是将工序分配给多人来完成的生产线,因此其希望达到各个工序能够同步、快节奏地产出,这样就会避免部分作业人员的工时损失,最终的结果就是产出最大化。我们常常用木桶理论来形容生产线的编排,要求所有的木片高度都一致,如果有一片低的话,水桶的水位(产出)就会取决于这一木片(工位)的能力。
也因为如此,我们流水线管理一定要想办法将每个工位的产出速度规划或督导至一致,否则,则会出现产出不均衡、工位堆积、人员闲置等待等现象,最终影响的是成品的产出数量。
3、 基础IE手法在流水线改善中的应用
基础IE手法源自100多年前以泰勒及吉尔布雷斯等工业工程前辈研究并实践的改善手法,主要指的是工作研究及动作研究,我们经过总结归纳将常用的改善手法,从其应用的范围又分为程序分析、作业分析、动作分析及时间观测。而恰恰这几个方面在流水线生产的改善过程中,无论是从宏观面分析还是从微观面改善,都对流水线的效率提升有着良好的作用。
3.1 关于时间观测的应用
相信对于工时,所有搞生产管理的朋友都不陌生,任何关于时间及产出的用词都能够随口而出,但大家对于科学化制定标准工时,却不一定人人都能够掌控。
在基础IE里面,我们需要对每一个工作站进行工时测定,工时的制定是有要求的,如其必须要具备客观性、可测性、适用性,以及工时产能的制定前提是作业方法应当是透过作业研究形成最佳的,否则会造成工时数量不准确,不仅起不到良好的标准制定,更无法促进改善的推动。另外我们需要透过工时的测定来编排或优化新旧产品的排位,如果工时不合理,则编排出来的工位其合理性也很难保证,更谈不上高效化体现了。
3.2 关于程序分析的应用
学过程序分析的朋友都知道,程序分析是基于一个过程的分析,包括如工艺流程分析、作业流程及线路图分析。流水线本身就是一个过程的最完整表现,因为它是多人组成从头到尾一工序接一工序实现的,所谓环环相扣就必须要实现流程的同步化、均衡化。
通常我们在生产线编排或优化前,会先利用工艺流程图的方式将所有工序之间的联接关系给整理出来,这样就能够一目了解地知道工艺顺序,对于工位的合并或调整起到直观的参考作用。
然后再利用作业流程分析表的方式,将每个工序的工时加以分析,进行平衡性工序调整分摊,最终实现不同工序的人员工作量尽可能一致。
最后形成作业排位图(线路图),将不同工作站在流水线中的位置、物流方向、必要的人员走动轨迹及其它物品放置等表现出来,这样有利于生产线快速转款。
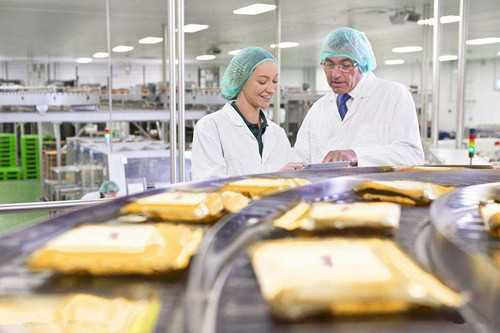
3.3 关于作业分析的应用
作业分析区别于程序分析的宏观性,强调某一个工作站的分析,不管是对于瓶颈工序,还是一般性工序,都能够透过分析改善提高效率。作业分析包括:双手作业分析、人机作业分析及联合作业分析。
先谈谈双手作业分析,这个是装配业最广泛的应用手法,有人的地方,必有手工作业,透过双手作业的分析方法来实现动作浪费的识别,然后再透过双手动作的优化来提高效率。
再谈谈人机作业分析,我们有很多生产线的工位是由设备组成,甚至是由1人操作多台设备,该设备往往由于与人作业的交互不佳而形成瓶颈影响产线效率,故我们可透过人机分析的方式来优化工位产出。
最后再说联合作业,像很多生产线最后一道工序为包装作业,产品稍微大点儿都可能需要两人以上合作完成,这种多人配合的作业,会不会因为工序分配不佳而影响整个作业周期,我们可以透过联合作业分析来实现分析及改善。
3.4 关于动作分析的应用
最后谈谈最微观的动作改善,我们在做动作改善时常会与前面的双手作业改善混淆,因为两者都会表现在人的双手上,不过动作改善不仅仅是双手,而是全身都会涉及。
我们有时候会轻视动作改善,认为动作是一个很微小的时间单位,对产线的效率影响不大。那么我们可以去看看一些电子厂,或者大批量作业的生产线,他们的产量动不动就是每小时2000甚至更多,计算下来也就是一点几秒产出一个产品,在这种情况下,可以想象到一秒半秒对于产线的影响是多在。
动作改善主要是透过对工位进行动素拆分,来识别有效动作或无效动作,然后再利用动作经济原则的三大改善方向,最终实现工位的效率提升。
上述基础IE手法在流水线中的应用,主要是希望能够从生产前的规划,到过程中的优化,都能够利用科学的方法来实现,这样会更有利于效率提升与保障。
文章来自网络,版权归作者所有,如有侵权请联系删除